Minimize Machine Downtime
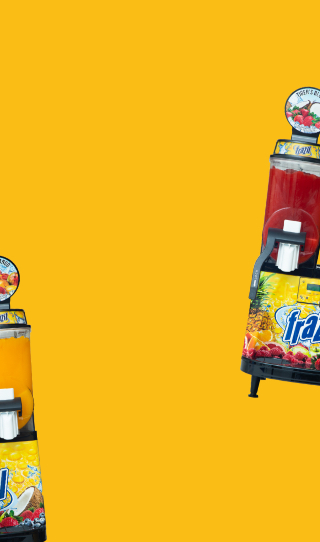
Downtime on revenue generating equipment can be expensive. Every week a machine is down it may cost $200 or more of lost revenue depending on how busy your location is. Our data shows that several locations may wait 2 weeks or more before calling for a machine to be serviced. While a fast response to a machine needing service is critical, it is best if to prevent the equipment from going down in the first place. After years of experience working with thousands of BUNN ULTRA machines, we have developed simple prevention steps any retailer can follow to minimize machine downtime.
Clean The Machine Filter:
A dirty filter is the number 1 problem with a machine that is not freezing. 30% of the service call requests we receive from customers reporting a machine not freezing are due to a dirty filter. This is preventable simply by cleaning the filter regularly, like cleaning out the lint from your dryer at home. The machine has to breath to work properly. On a BUNN machine, the filter is the entire rear of the machine. You can remove the filter by pulling down, out and up using the two tabs on the filter. Wash the filter under water until the water runs clear. Then replace the filter by placing the bottom in the bottom track and snapping back into place. We recommend that the filter be cleaned every 15 to 30 days. You can watch a training video here on how to clean a filter on a BUNN machine.
Keep The Machine Full:
Running machine with low product will cause overheating and damage to the machine’s motor. If you can see the white auger and metal cylinder the machine is low and should be refilled. You can manage busy times by keeping a supply of pre-mixed product in the refrigerator. Cold and pre-mixed product takes less than a minute to add and freezes down very quickly. For Frazil customers, we will supply additional mixing jugs to Frazil retailers at no cost to help facilitate this. Additional mixing jugs for Frazil customers can be ordered here.
Mix Product Correctly:
Using different ratios of product to water may keep the product from freezing properly. If one or both sides of your machines’ product is not freezing, it may be the result of the product not being mixed correctly. Too much sugar to water is often the cause of freezing between bowls also.
Review and follow product mixing instructions. For Frazil, the mixing instructions are printed on the back of each package and the front of each mixing jug. The ratio is one mixing jug of water to one pouch of product. Pour the contents of the package into a clean Frazil mixing jug and fill partially with water. Shake until the mix is completely dissolved. Finish filling the mixing jug with water and shake until the product is thoroughly mixed. Pour product into the frozen beverage machine or refrigerate after mixing. Additional mixing jugs for Frazil customers can be ordered here.
A helpful hint is to keep at least two gallons of ready-made product in the cooler, this allows for a quick refill of the hopper. The colder the product when you add it to the machine the faster it will freeze. You can watch a training video here on how to properly mix product.
Properly Place and Replace Seals: Leaking product is messy, wasteful and may eventually lead to your machine going completely down. Tank or hopper seals and faucet seal leaks are easily preventable. We recommend that faucet and tank seals be replaced around every 6 months. A retailer can easily replace both a faucet and tank seals. Frazil bundle customers can order replacement faucet and tank seals here.
Other ways to prevent leaks include avoiding a pinched tank seal. Ensure the tank seal is flat and has not been pinched when the bowl is put onto the machine. A pinch often occurs when the store representative reapplies the hopper after cleaning.
Before filling a hopper or bowl with product, it is helpful if you first check for a pinched seal by filling it with water above the area in the bowl that the tank seal covers to make sure there are no leaks. Water is a lot less messy to clean up if there is a pinched seal and will not result in any lost product. Once you are positive there are no leaks, drain the water from the machine.
If the tank seal is not pinched and properly placed and the machine is still leaking, check if the tank seal is damaged or dirty. Inspect the tank seal for any tears. Clean the tank seal. If the leak continues, the tank seal will need to be replaced.
Another preventable leak root cause is when the machines’ cylinders (the silver rods on the machine) get out of alignment. This usually happens when the machine is lifted using the cylinder vs. lifting from the base of the machine, typically while removing and replacing the hoppers during cleaning. When cylinders are out of alignment, this may cause a leak from the back of the hopper. You can prevent this by properly lifting or moving the machine without using the cylinder. For a BUNN ULTRA machine, if this has happened, please correct the problem by pushing the cylinders down gently. The center of the shaft should be four and a half inches from the lowest point of the upper drip tray or attach the auger and push down on the cylinder until the auger touches the base.
Please note that it is normal for a machine to leak water. This is called sweating and should not be cause for concern. You can watch a training video here for ideas on how to prevent and even troubleshoot leaking and loud machines.
Properly Set Product Thickness: On a BUNN ULTRA unit you can change the product thickness level. Thickness levels should be set at 8. If not, it may result in the product not freezing or over freezing causing an inferior customer experience that may lead to a service call to fix something that can easily be prevented. For a BUNN ULTRA unit, press and hold the ‘Gourmet’ button for 6 seconds to access the menu. Navigate through the menu by pressing the “Gourmet” button until you arrive at the second menu option titled ‘set thickness.’ Verify the thickness level is set to 8 for both the left and right side. You can watch a training video here on how to adjust product thickness levels.
Set Nighttime Mode to Run Daily: It is important to set nighttime mode to avoid freezing between barrels and undesirable product color and consistency. To prevent this, nighttime mode should run for at least 2-4 hours each day, even if the store runs 24 hours a day. We recommend setting nighttime mode from 2 am to 6 am. You can watch a training video here on how to adjust nighttime mode settings.
Other Common Downtime Prevention Ideas:
- Do not overfill the hopper or bowl. Product should not exceed the max fill line. This may result in product on the top of the bowl not properly mixing and over freezing.
- Make sure the unit has a dedicated circuit, the breaker is not tripped, the machine is plugged in, and the power is switched on. Also, make sure the machine setting is placed in freeze mode. For the BUNN ULTRA, you can identify if the freeze mode is on by ensuring the screen shows “ICE” in uppercase lettering for both hoppers or bowls.
- Give the machine at least 6 inches distance from the back of the machine and the wall to breathe otherwise the product may not freeze properly.
- Ensure the placement of the machine is not in direct contact with sunlight or a heat source that is counterproductive to freezing.
- If lights are blinking, ensure the machine is full of product and the sensor probe is inserted correctly into the hopper or bowl (if the machine has a sensor probe).
You can watch training videos here and here that covers these other common machine downtime prevention ideas.